Choose the Right Lubricant and Supplier | Select lubricant based on equipment type and factors such as temperature, load, speed, and environment. Choose an experienced, OEM-approved lubricant supplier for guidance and support. |
Lubricant Quantity | Use the right quantity of lubricant to prevent damage to equipment. Avoid over-lubrication to prevent early wear and tear. |
Apply Lubricant at the Right Time and Place | Follow a lubrication schedule based on supplier recommendations and operational requirements. Apply lubricant to specific spots on the equipment for optimal functioning. |
Keep an Eye On the Lubricant’s Condition | Perform regular oil analysis to ensure lubricants are in good condition. Take corrective actions based on analysis results to prevent harm to machines. |
Appropriate Storage and Handling | Store and handle lubricants properly to retain integrity and efficiency |
Control Contamination | Maintain lubricant cleanliness to prevent equipment damage. Use filtration techniques to remove contaminants. |
Regular Monitoring | Monitor lubrication program efficiency through performance reviews and inspections. Use condition monitoring techniques to address issues and increase equipment reliability. |
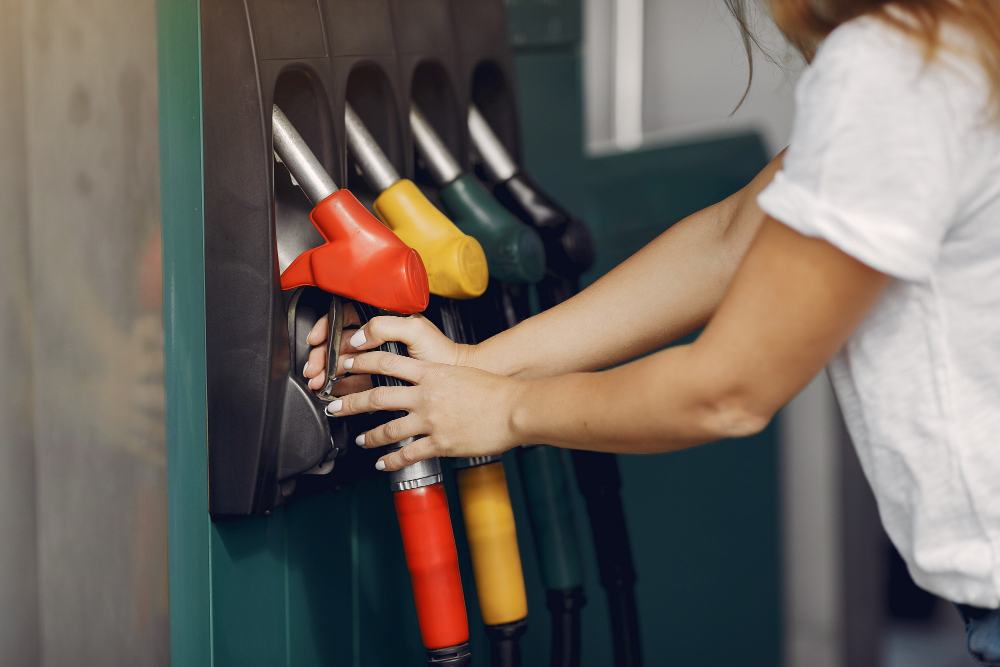
7 Steps to Effective Lubrication Management
Lubricants are essential for decreasing friction, heat, and wear between moving parts, preventing costly breakdowns, and improving overall efficiency. Follow these steps to achieve the best outcomes:
Choose the Right Lubricant and Supplier
Lubricants are available in a wide range of types; choosing the right lubricant depending on the equipment type is essential. The most common lubricants are in the form of grease and oil, with several variations. The oil lubricants can either be mineral or synthetic, having a wide range of viscosities.
Each form of lubricant comes with a different additive range and is designed for specific applications. The same type of lubricant is not required for all machines and equipment. When selecting the correct lubricant, factors such as operating temperature, load, speed, and environmental variables must be considered.Â
It’s equally important to choose an experienced, well-trained, and OEM-approved lubricant supplier who provides the right instructions and tools required during the process. He will guide you on which lubricant you should use and which to avoid.
Be Mindful About the Lubricant Quantity
When it comes to the lubricants, the less is the best. Excessive products can cause damage to your equipment. Using the right quantity is important for the effective protection of moving parts of the machines. Over-lubrication can be harmful as it can lead to dirt and dust accumulation, necessitating more maintenance and causing early wear and tear.
Apply Lubricant at the Right Time and Place
Lubrication on a regular and timely basis helps to minimise excessive wear and tear on components, lowering the likelihood of breakdowns. Failure to adhere to lubrication schedules can lead to increased friction, which can lead to increased energy consumption and decreased efficiency.
Create a lubrication schedule based on the supplier’s recommendations and the operational requirements of the equipment. Some machines, particularly those subjected to extreme operating conditions, may necessitate more regular lubrication. Following a well-defined lubrication scheme will improve machinery performance and reduce downtime.
Moreover, it is also critical to apply the lubricant in the right place. To maintain optimal functioning, certain components within equipment require lubrication on specific spots. You can get help from lubrication charts and manufacturer equipment manuals to learn about proper lubrication spots. Carry out regular inspections to ensure that the lubrication points are correctly identified and serviced.
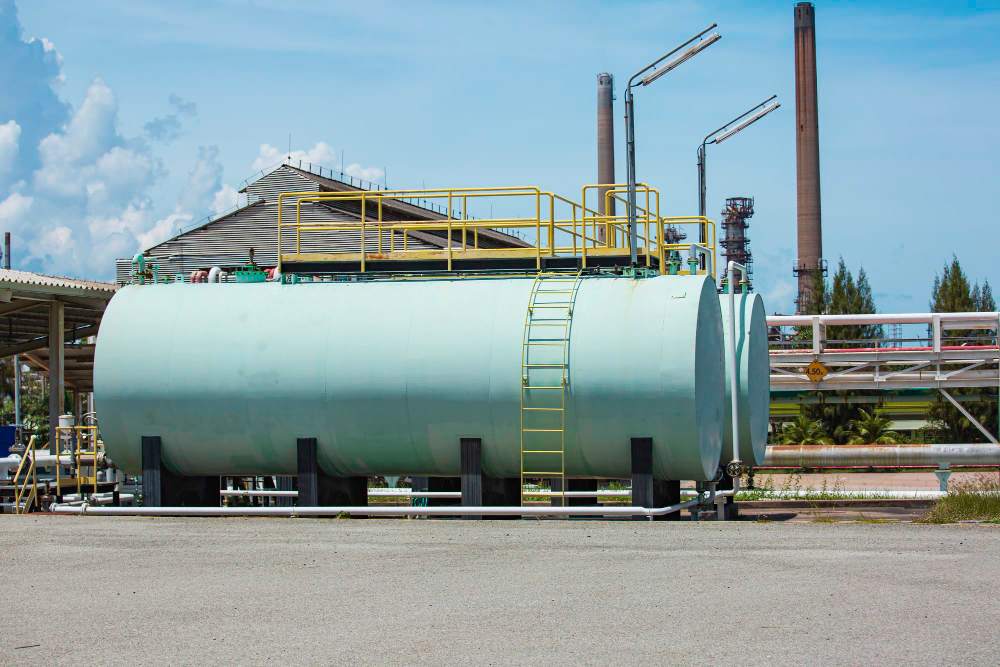
Keep an Eye on the Lubricant’s Conditions
The lubricant’s condition is just as crucial as choosing the correct lubricant. Lubricants can deteriorate over time due to variables such as oxidation, contamination, and heat degradation. Using deteriorated or contaminated lubricants might undermine their protection and, in some situations, harm machines.
Regular oil analysis should be performed to ensure that lubricants are in good condition. Oil analysis entails assessing the qualities of the lubricant and identifying any symptoms of degradation or contamination. Corrective steps, such as changing the lubricant or adopting appropriate filtration methods, might be made based on the analysis results.
Appropriate Storage and Handling
Lubricants must be stored and handled properly to retain their integrity and efficiency. It will help prevent lubricant degradation and contamination and keep its performance and quality intact.
Control Contamination
It is the most important aspect of an effective lubrication management system, which involves maintaining the lubricant’s cleanliness.Â
Follow these steps for cleaning lubricants:
- Examine the cleanliness level for each machine and follow maintenance practices to restrict the contaminants entrance.
- To remove the existing contaminants, you can use different kinds of filtration techniques.
Regular Monitoring
Monitoring the efficiency of your lubrication programme is critical for identifying possible problems before they become serious ones. Performance reviews and regular inspections can help you identify the contamination of lubricant, temperature changes, and equipment vibrations. These indicators may suggest a lack of lubrication, breakdown, or other concerns that must be addressed.
To get insights into the health of your machinery, consider employing condition monitoring techniques such as vibration analysis, thermography, and wear particle analysis. You may address lubrication-related issues and increase overall equipment reliability by using advanced monitoring tools.
Conclusion
Lubricant management is a vital element in ensuring the effective and reliable operation of industrial machinery and equipment. You can increase the lifespan of your equipment, minimise downtime, and maximise productivity by utilising the right lubricant selection process, using lubricants in the right location, at the right time, and under the right circumstances, and implementing proper monitoring. A good lubricant management programme not only saves money but also helps to create a safer working environment.